Hose pumps
Transfer and dosing with maximum efficiency and durability
Heavy-duty pumps with XXL rollers
Design featuring built-in bearings to work in the toughest conditions.
No friction
Saving in energy consumption of up to 30%, and lower maintenance costs.
Latest generation peristaltic hose
High quality hose with a unique manufacturing process. Extruded interior and ground exterior to ensure optimum compression
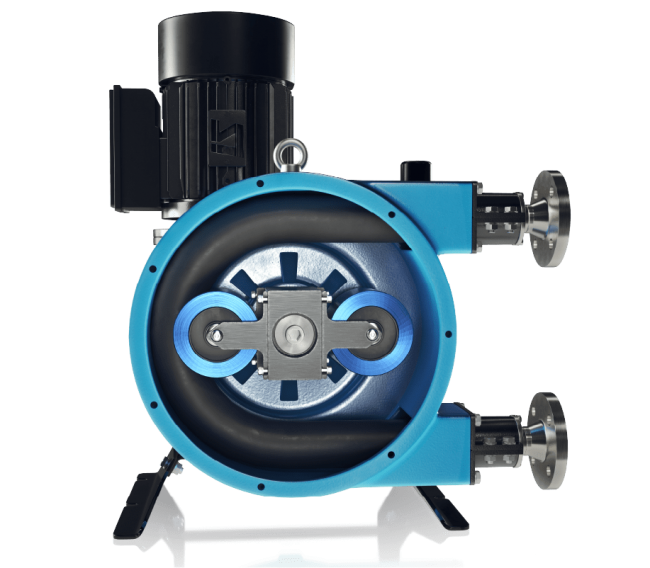
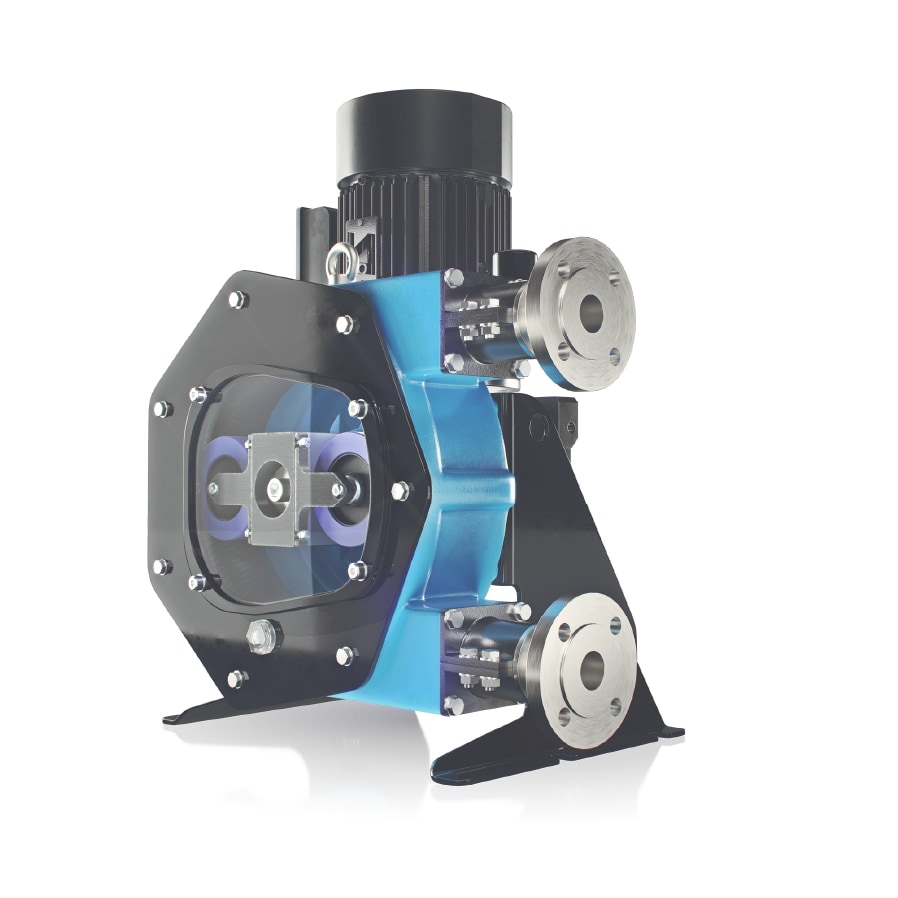
Built-in bearing system
All PeriBest pumps have built-in bearings that absorb loads on the shaft when the hose is compressed, thereby relieving the gearboxes of these loads and extending their longevity.
Protective seals
All the bearings we use are sealed and lubricated for life. They are further protected by external seals, which maximise their durability.
Extra large bearings
Both the shaft bearings and the roller bearings are extra large to ensure that they work well, even under the most demanding load conditions. Thanks to this design, our rollers never block, even when working at high pressures.
Long component life
The materials selected and design are focused on the strength and longevity of the pump. As a result, the only component subject to wear and tear over time is the hose.
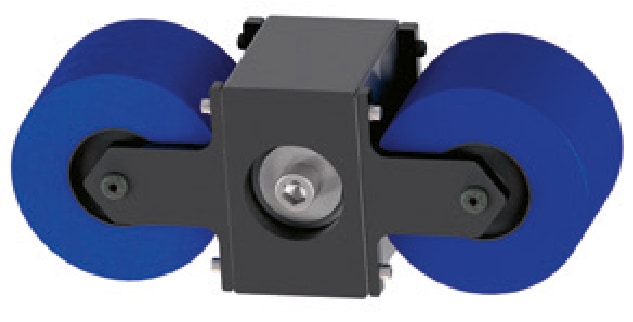
Very large roller system
The only roller pump capable of operating at pressure levels similar to shoe-type pumps, thanks to a much larger contact surface than a traditional roller system.
Up to 30% power saving
The rollers rotate smoothly on the hose, without the typical friction caused by a non-rotating component such as a shoe. Both the shaft bearings and the roller bearings are extra large to ensure that they work well, even under the most demanding load conditions.
Special hard aluminium alloy
The rollers are made of a special hard aluminium alloy, which is the same as that used in the shoes of traditional peristaltic pumps. The useful life is extended thanks to this high-strength material and the lack of friction between the roller and the hose, meaning that the hose is the only component subject to wear and tear.
Ease of maintenance
Despite being very robust, the rollers are very light. This, together with the innovative design of the pump, makes it easy to dismantle in order to change the hose. The lack of friction reduces the amount of lubricant required by 90%, which substantially reduces maintenance costs and the waste produced.
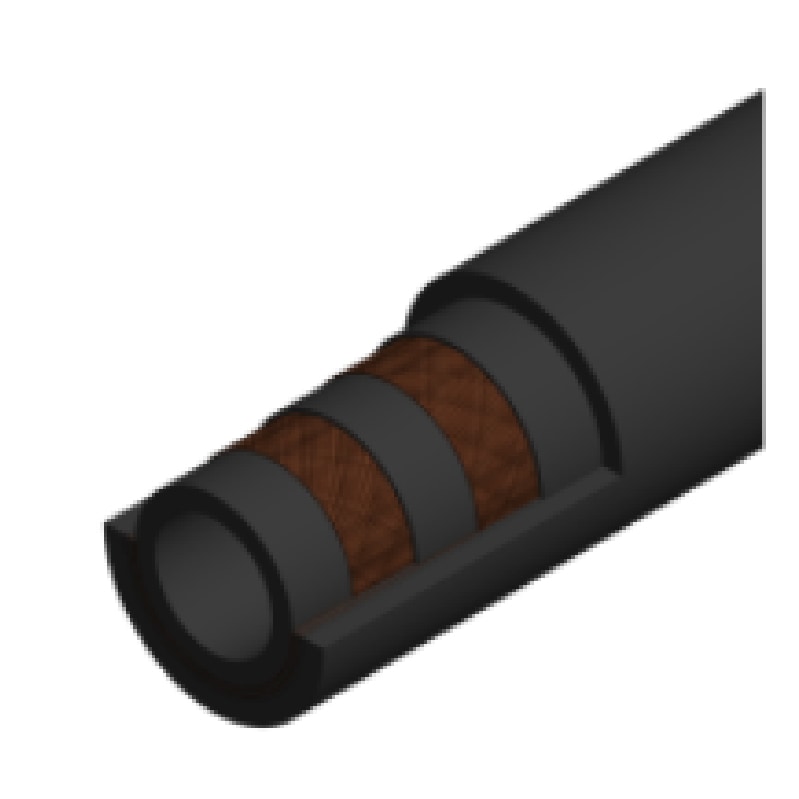
PeriBest's unique, proprietary manufacturing process
Every part of the hose (inner part, textile reinforcements and outer part) is carefully manufactured to ensure that it will outlast its competitors. This innovative process combines the best of those used by other manufacturers.
Highest demands in terms of quality
The fact that the hose is the only component subject to wear and tear means that it is a key part when it comes to optimising performance and costs. The materials used to make PeriBest hoses are of unprecedented quality, thanks to the machinery used and the quality control of the manufacturing processes.
Very tight tolerances
Both the inner and outer diameters of PeriBest hoses have very tight tolerances. This is done through a grinding process that can achieve tolerances of +/- 0.2 mm. This precision ensures the optimum compression of the hose, freeing it from excessive stress and making high repeatability possible.
Reduction of downtime
The durability of the hose not only reduces costs due to the savings on the material itself, but also, because it breaks so infrequently, the number of times the pump has to stop working to replace the hose is drastically reduced.
Extremely robust design for the most demanding applications up to 10 bar.
Dosing of all kinds of corrosive chemicals.
The best solution for dosing and transferring all types of acids and corrosive products and products with a high solids content of up to 80%.
Hose leak sensor and drainage system included in the chemical version and optional in the other versions.
Technical specifications
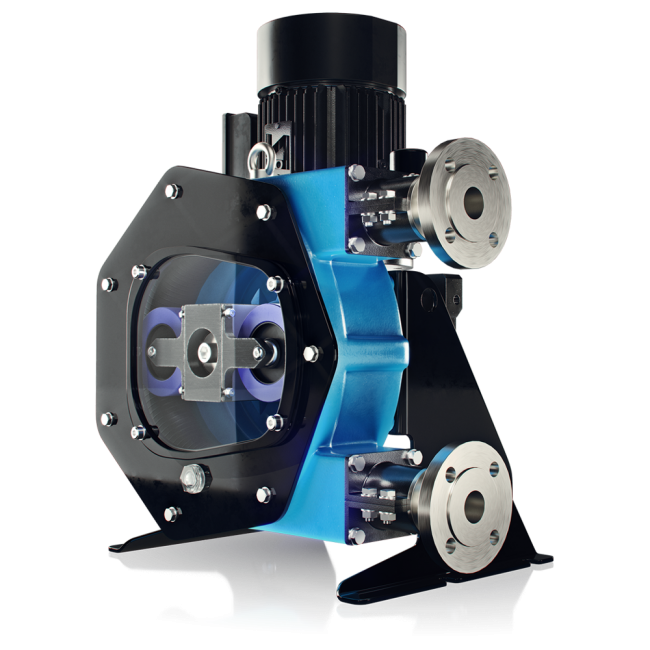
FLOW RATE RANGE 5 to 20.000 l/h
MAXIMUM PRESSURE 10 bar
INNER DIAMETER 13 to 70 mm
MATERIAL OF CONNECTIONS AISI-316, PP, PVDF (PTFE)
CONNECTION TYPES BSP, DIN, NPT, ANSI
MATERIAL OF ROLLERS Hard aluminium (anodised)
MAX. TEMPERATURE 80ºC
MATERIAL OF HOSE NR, EPDM, NBR (Food grade) and Hypalon (up to model 21)
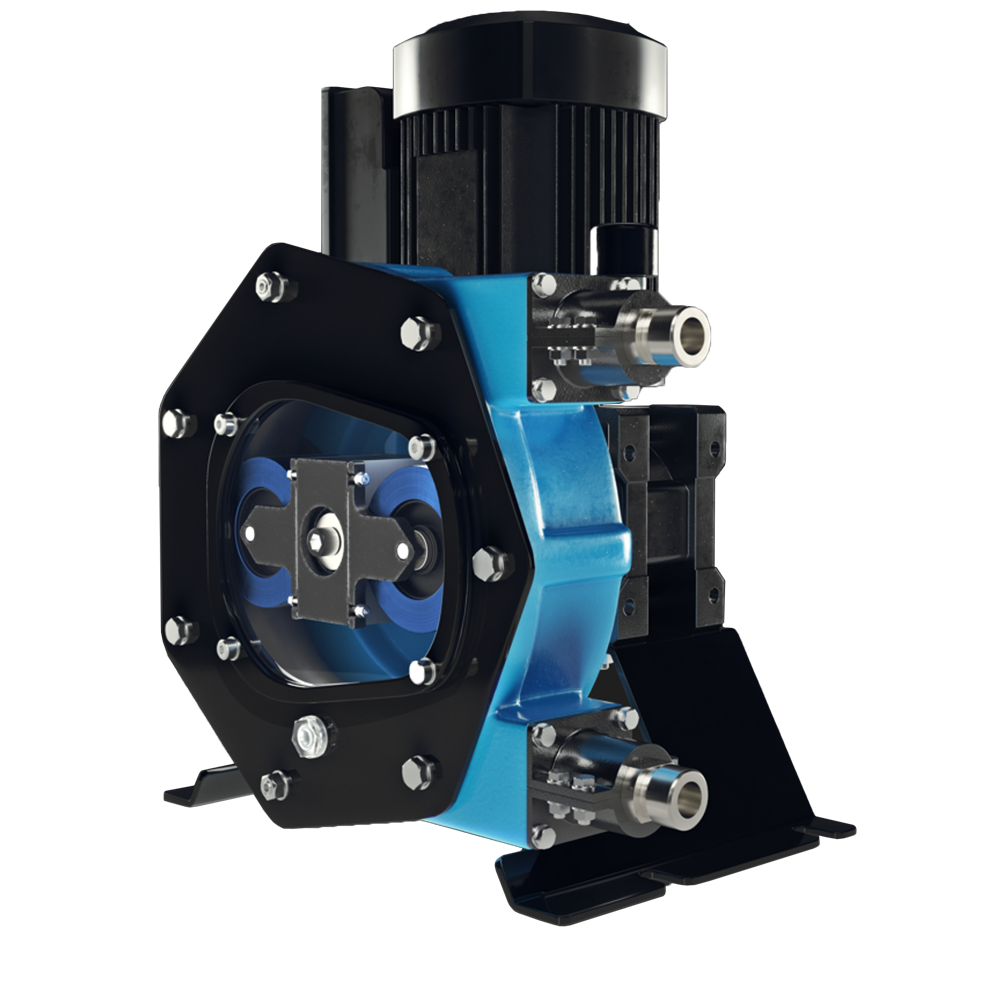
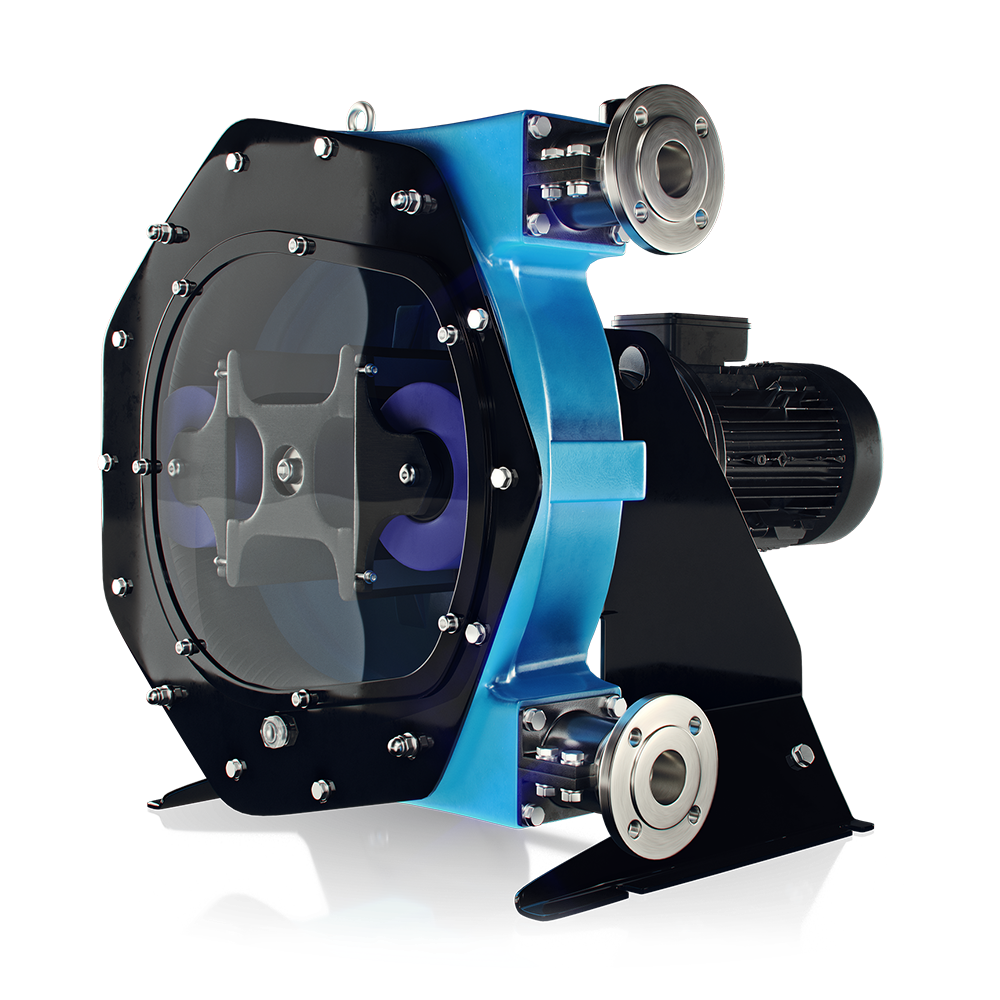
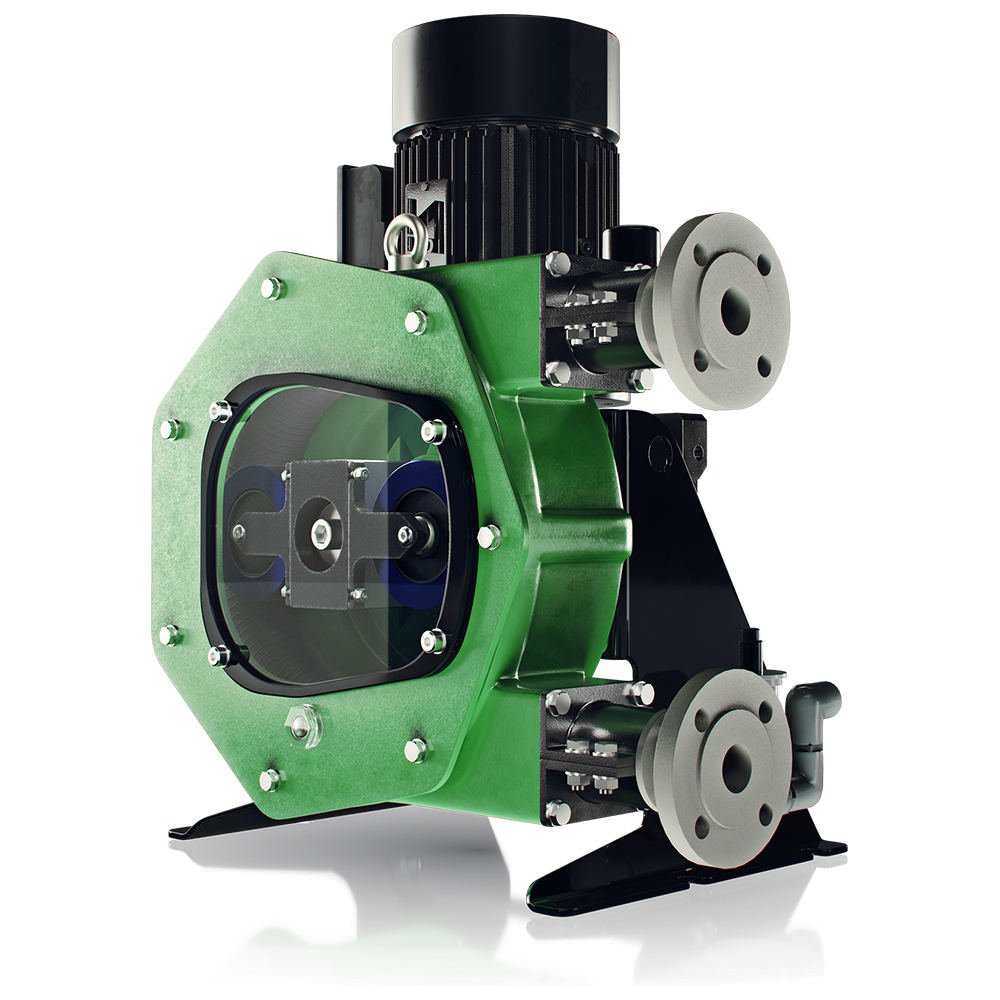
The best solution for dosing corrosive products.
Go to section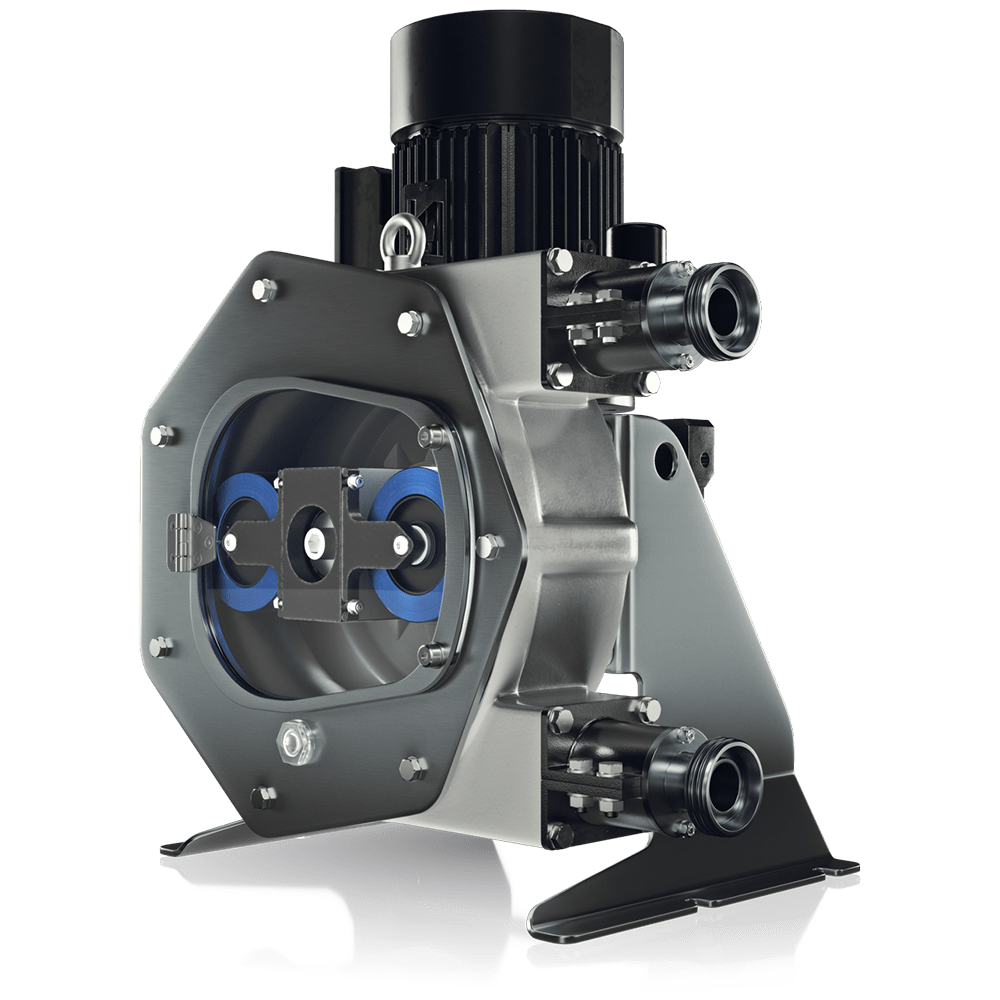
A new concept for the pumping of food products.
Go to section